Choosing Your Toolpath Strategy for 5-Axis Machining
CAM systems have a diverse selection of toolpath strategies to choose from, and each has an appropriate place in 5-axis machining. But just like everything else in multi-axis programming, the programmer's experience and the actual machine configuration will play a big part in the selection of the suitable toolpath for a particular application.
Toolpath Factors
If you ask 10 different programmers to program the same part, the outcome is likely to be 10 completely different machining strategies. Other factors, like the number of pieces to be machined, the allotted time for completing the project, the specified material and available tooling, can also play a significant role in the toolpath selection process; but the skill level and experience of the programmer will always have the greatest impact.
Toolpath and Simplicity
Curve multi-axis, swarf cut, flow line, multi-surf, port, rotary — which toolpath is the correct one? While each of these choices have something substantial to offer, most programmers over time will gravitate to one or more of these as their favorite go-to solutions for 5-axis programming. However, no matter what part you are programming or what industry you are working in, one rule always rings true when selecting a machining strategy: K.I.S.S. (Keep It Simple Stupid). This acronym can be applied to many things in life, and selecting NC programming strategies is certainly one of them, especially 5-axis strategies!
Although complicated simultaneous 5-axis machine movement is cool and exciting to watch – and typically what people envision when you mention 5-axis machining – you are usually best served to steer clear of it if possible. With all five axes moving at one time while the tool tip is buried deep inside features on the part and the tool body and tool holder are constantly tilting and moving closer and closer to the workholding device and machine structure with every pass, you can see how quickly the stress level can skyrocket for the poor machine operator who drew the short straw and is in charge of proving out the first run of this scary process.
Now, you might ask yourself, if simultaneous 5-axis isn’t the answer, then what is? The answer is 5-sided or 3+2 programming.
5-sided programming
Although there are definitely some products, such as impellers, that simply require simultaneous movement to allow the tool to reach complicated features on the workpiece, the vast majority of parts can be successfully machined by simply using the two additional rotary axes to position the part at some designated angular orientation. Then you can employ a simple 3-axis toolpath to machine the necessary characteristics. Not only is this a simpler and safer approach, but the resulting cycle time will be shorter as well. When programming 5-axis simultaneous processes, machine movement is always limited by the speed of the slowest rotary axis. However, when the rotary axes are only used to orient the part into position, then the remaining linear axes of the machine are capable of cutting at the fastest maximum feedrate allowable by the control without regard for the limitations of either rotary axis.
The 5-Axis Advantage
It is also worth mentioning that just because you’re not using simultaneous strategies and are only employing simple 3-axis toolpath technology, you can still take advantage of the obvious reduction in multiple setups and benefit from many other characteristics most associated with 5-axis machining. For example: when using the rotary axes just to position the part for machining, nothing dictates that the tool axis angle must be perpendicular to the surface being machined. Positioning to a non-perpendicular orientation will allow you to cut on the corner radius of a ball or bull-nosed endmill, and therefore achieve the high-quality surface finish and chip load control that is most often a desired outcome when moving to a 5-axis machine.
As I mentioned in a previous blog article (5-Axis Machining: It Just Ain’t That Scary), just because this technology is advanced doesn't mean that needs to be over complicated. Applying the K.I.S.S. system to your approach and formulating a well thought out plan before you begin multi-axis programming is really quite a simple concept.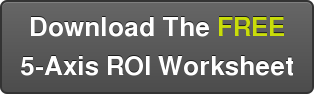
You'll find more helpful resources, such as training videos and webinars, at Hurco Connect.
Don't forget to subscribe to the CNC Machining Blog! You'll receive an email notification whenever a new post is published.