Absolute Tool Length for CNC Machinists
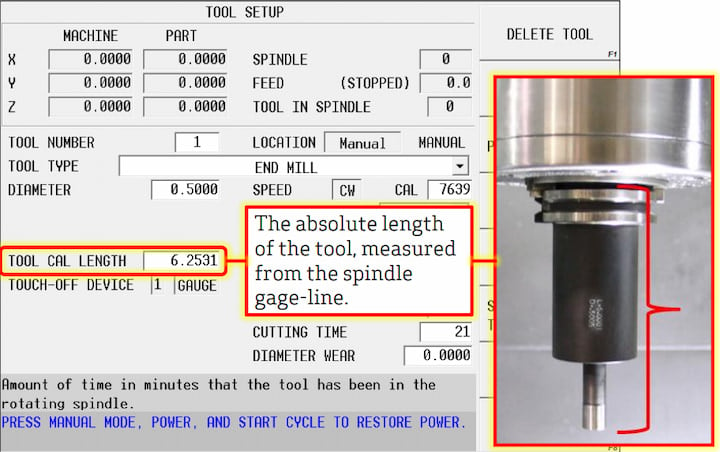
Absolute Tool Length is an industry standard feature in CNC machining that provides continuity across machine brands and controls.
Absolute Tool Length is an industry standard feature in CNC machining that provides continuity across machine brands and controls.
Hurco CNC machines are built for the long haul thanks to their robust iron that will last a lifetime if maintained properly. We love to highlight customers who are still making money with vintage Hurcos that they purchased back in the 1980s and 90s. Bryant’s MachineShop is a great example.
Anyone who runs a 5-axis CNC machine knows how important correct centerline measurements can be for accurate machining. Often times, however, when troubleshooting for issues, or after a slight “bump” of the machine, there might be a need to verify or re-measure these centerline values.
One of the features of Hurco that many customers love is the eight-nozzle coolant ring that comes standard on all VMX models of vertical machining centers. The amount and flow of the flood coolant is sometimes unbelievable to many new users. Now Hurco VM owners can experience this same overwhelming feeling of flood coolant!
A while back, I received a comment on one of my previous blog posts asking how to designate 5-axis transform planes using IJK UVW vector tokens instead of the traditional ABC rotary axis designations on their 5-axis CNC machine. Instead of just replying to that comment, I thought I would write this post as a response. Since this will be a continuation of the 5-axis CNC basics series, I suggest that you read and understand using IJK tool vectors as a pre-cursor to this article.
The idea behind creating a 5-axis transform plane using vectors is exactly the same as programming tool movement with IJK tool vectors on any machine with a fifth axis. However, the difference lies in the fact that you will have two separate vectors: one using IJK and the other using UVW. The reason you need two separate “legs” for this function is because you cannot designate a plane with only one axis. I will use the floor inside a room as my analogy: you could not create a floor in a room without having at least two walls. With only one, the floor would simply spin around that single axis and could actually point in literally any direction. To accommodate the two legs of the transform plane, and because we want to determine the direction of the Z-axis ultimately, we will use the X-axis and Y-axis as our legs, or walls of the desired transform plane.
Today’s Hurco users are well aware of the term SFQ, or Select Surface Finish Quality, on the Hurco control, and probably have a pretty good idea about which settings work best for them – however, many of them probably don’t realize what is actually going on behind the scenes, and what those settings actually mean or how they affect the machine’s behavior.
Over the years, Hurco has partnered with many tooling companies. Recently I received a link from G.W. Shultz, that showed a video of one of thier tools cutting 422 Stainless Steel, on a Hurco VMX30HSi High Speed milling machine - at some pretty impressive speeds. The information listed in the video comment section says: "Pushing the G.W. Schultz Tool HGW40250-01 to 1000SFM in 422 Stainless Steel".
PUBLISHED: NOV. 7, 2014
UPDATED: AUG. 3, 2023
When people hear the term “automation,” it usually conjures visions of high-production processes, where shops are running hundreds of thousands of the same part. But in today’s ever-changing and increasingly competitive industry, that is not always the case. Just like many small job shops have begun to migrate toward 5-axis machines to increase multi-sided part efficiency, those same shops are also beginning to move toward automation to help them increase profits.
To understand and begin this migration toward automation, you first must understand and buy in to the ideas of standardization and palletization. Winning in the game of high-mix, low-volume part manufacturing means reducing spindle downtime. The first step towards winning that battle is standardizing your setup process. At the end of the day, you can only invoice for the parts that you have completed. So, reducing idle time between jobs is a crucial step to getting more done in a typical eight-hour shift.